Reduktion von Ausschuss in der Produktion durch Inline-Sensorik verknüpft mit KI-Modellen
Das Projekt INTEUM, gefördert durch das Bayerische Verbundforschungsprogramm (BayVFP) mit über 900.000 Euro, zielt darauf ab, durch den Einsatz von KI-Technologien und präziser Inline-Sensorik die Effizienz in der Produktion bei Stanzwerkzeugen zu erhöhen. Im Fokus steht die Entwicklung eines intelligenten, echtzeit- und transferfähigen Messsystems auf Basis von Acoustic Emission, das durch Produktionsplanungs- und Maschinenüberwachungsdaten (Condition Monitoring) gespeist wird. Projektträger: VDI/VDE-IT (DIE-2108-0006//DIE0156/01).
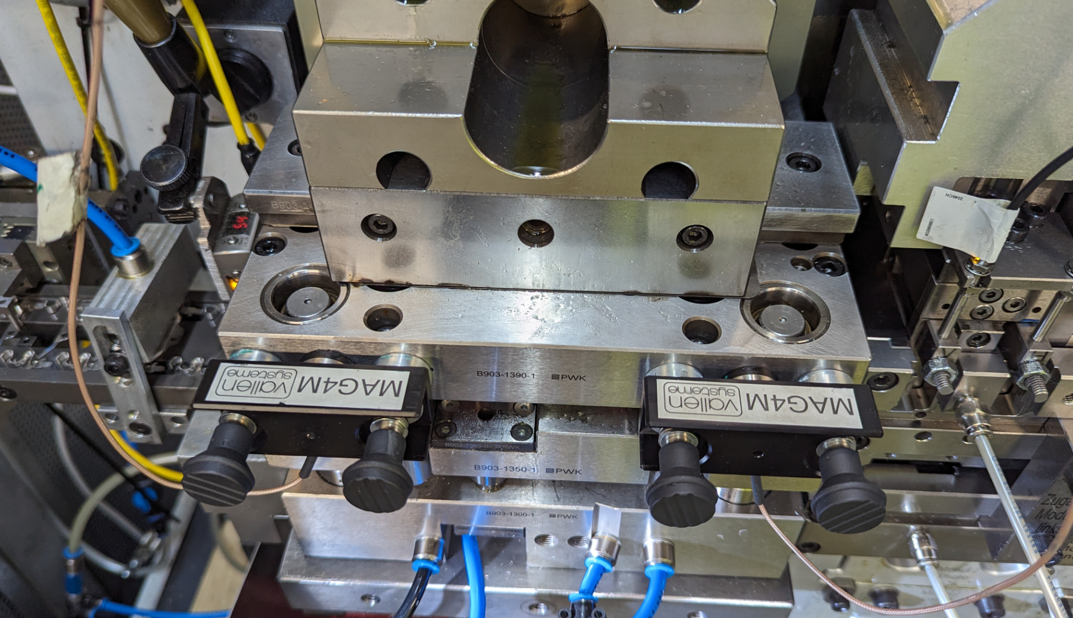
Problem:
Ein zentraler Teil des Produktionsprozesses bei Scherdel ist das Werkzeug, welches erheblichen Einfluss auf die Produktqualität und Stillstandzeiten der Maschine aufgrund von Wartung und Werkzeugwechsel hat. Wie lange mit einem Werkzeug produziert werden kann, ist dabei abhängig vom Hersteller und wie das Werkzeug aufgearbeitet wurde. Diese Risiken wurden bisher anhand von starren Wartungsfenstern und Maßverläufen der Produkte abgeschätzt und gemanagt.
Motivation:
Durch eine kontinuierliche und autarke Überwachung der Werkzeuge und der Produktqualität lassen sich Anomalien, der Verschleiß und auftretende Schadensverläufe von einzelnen Werkzeugen in Echtzeit erkennen und zurückverfolgen. Auf Basis der erhobenen Daten lassen sich relevante Prozessparameter sowie Qualitätsmetriken anpassen.
Nutzen:
– Optimiertes Nutzen von Werkzeugen und Vermeidung von
– Werkzeugbrüchen Vorausschauende Planung der Werkzeugwartung
– Reduktion von Produktionsausschuss und Stillstandzeiten – Optimierung der Prozesssicherheit und -qualität – Effiziente Fehlerbehebung in Echtzeit – Minimierung von Energieverbrauch und Betriebskosten
Lösung:
Die Forschungsgruppe Cyber-Physical Systems des iisys (Hochschule Hof) entwickelte KI-Modelle zur Überwachung des Maschinenzustands und zur Predictive Maintenance. AMITRONICS stellte Hochleistungssensoren bereit, die die Schallemissionen der Anlagen registrieren. Zusätzlich durch die Verwendung von MQTT als Datenaustauschstandard wurden die Daten in Echtzeit weiterverarbeitet und Anomalien durch integrierte, intelligente Auswertemethoden identifiziert.
Scherdel stellte Anlagen, das dazugehörige Prozess Know-How, Planungsdaten und ihre IIot-Infrastruktur zur Verfügung, um die Identifikation und Behebung von Prozessrisiken zu optimieren. Neue Erkenntnisse zeigen, dass insbesondere Hochgeschwindigkeitsstanzen von dieser Technologie profitieren können.
Die Sensorik-Bayern GmbH brachte ihre Expertise im Bereich IIoT ein, übernahm die Retro-fit-Ausstattung der Maschinen mit Funksensorknoten und entwickelte Konnektivitätsmodule. Diese Sensoren lieferten Informationen zum Gesamtzustand der Anlagen und erkannten Anomalien im Produktionsprozess.
Durch Vibro-Acoustic-Monitoring (VAM) hat Scherdel die Möglichkeit die Werkzeuge optimaler zu nutzen und so entsprechend vorausschauend die Werkzeugwartung planen, um Ausschuss oder Werkzeugbrüche zu vermeiden. Die erfolgreiche Implementierung dieser Technologie könnte dazu führen, dass Scherdel sie auf weitere Anlagen ausweitet. Dies würde die Produktqualität erhöhen und den Energieverbrauch sowie die Betriebskosten senken, indem Ausschuss und Produktionsfehler frühzeitig erkannt und behoben werden.